THE USGA: FOR THE GOOD OF THE GAME.
In the winter season many of the games over 25 million golfers will do more than stay inside and keep warm.
It’s a time that the smart golfer uses not only to get better, but to make judgement’s about the equipment they use and if it’s time to upgrade what’s in the bag.
Everyone from the pro shops to the golf stores, will have a holiday deal just in time to get rid of the old stock and get ready for what’s coming in for the next year. In this case the 2015 products lines are arriving, if they haven’t already. A few companies hold off until the PGA Merchandise Show in Orlando, to release the new product line. That show tee’s off in January, a great time to get the golf industries players and more importantly the buyers to a warm climate to start the season.
Long before you see those products on the convention center floor, or in TV ad’s. They have been through a range of test’s in Far Hills New Jersey, home of the United States Golf Association (USGA).
Far Hills New Jersey is not only home to the USGA Museum,and corporate offices, but to the Research and Test Center that first opened in 1984.
What the RT Center is called upon to do, is support the USGA’s role in creating equipment standards for the game of golf.
Since first being built, the center has had two major renovations. It’s size has been increased to over 20,000 square feet, of both office and testing space. This area includes room for laboratory space as well as an outdoor testing range. The range is 325 yards long and is now 60 yards wide.
The USGA Testing Center is home to what the USGA calls the Equipment Standards (ES) Staff, which consists of 16 full-time employees. The staff is made up of engineers, technicians, and other professionals, who work with outside consultants and who have almost 275 years of combined experience at the USGA.
John Spitzer, is the Managing Director of the USGA ES staff. Spitzer who was originally hired by the founder of the center the famed Frank Thomas, has now been part of the R&T Center for 16 years after working in the Princeton University Plasma Physics Laboratory, General Dynamics Corporation, and Electric Boat.
The ES Department defines it’s mission as this. To maintain the challenge of the game by ensuring that player skill, not equipment technology, continues to be the dominant factor for success.
What the core functions of the testing center do.
The Core functions are to test, measure and evaluate submitted golf equipment to provide conformance rulings based on the language and intent of the Rules of Golf in a consistent, repeatable and timely manner. These functions include:
*Conduct relevant and accurate research on golf and golf equipment in support of creating conformance decisions and to provide relevant information to our audiences.
* Assist in the formation of equipment rule policies and strategies, and recommend equipment rule changes.
* Develop accurate and reliable tools and methods for testing golf equipment.
* Provide accurate, repeatable, and timely test services to equipment manufacturers.
* Coordinate rules, rulings, testing, and research with the R&A.
*Communicate with golfers, manufacturers, and the media regarding equipment evaluation and rules.
*Develop and distribute golf science and technology educational outreach programs or materials.
THE JOINT STATEMENT WITH THE R&A.
The ES Staff is guided in its mission by a Joint Statement of Principals that was established in 2002 in cooperation with the Royal and Ancient Golf Club of St. Andrews (R&A). The Joint Statement of Principals acts as the framework which guides the actions for the formulation and enforcement of equipment rules both now and in the future. As the governing authorities for the Rules of Golf including equipment Rules, The R&A and the USGA continually monitor the effects of advancing equipment technology on the playing of the game.
Before the golf products even make it to the testing lab, they spend time in a large storage area that is loaded with products that have been tested, will be tested or retested.
The Test Center gets over 2,000 equipment submissions each year that include, full clubs, clubheads, shafts, gloves, tees and other items such as shoes. This total does not include the more than 1,300 different brands of golf balls submitted for conformance testing to the USGA each year. Golf ball submissions grew from about 800 in 1999, to almost 1,400 in 2013. Clubs and other devices grew from around 750 in 1999, to almost 3,400 by 2009.
A golf ball manufacturer that would like their product placed on the Conforming List of Golf Balls, must submit to the USGA at least, two dozen balls of each brand they want tested. The ES Staff tests some 30,000 golf balls, through a variety of ways. The USGA will then visit tournaments and request a sleeve of balls from players using new types on tour, just to make sure what the company is sending to the USGA, is what they are giving their staff players on tour according to Spitzer.
The balls get measured for size and weight. Then they are put through tests to determine an initial velocity (IV). These tests are performed in a climate controlled lab, to make sure all balls are tested in the same temperature and humidity. From there the next step is to check the distance standards. Until a few years ago, all tests were done outside on the test range. Now that has been changed because of outside temperatures, wind speed and conditions of the turf the balls land on.
As a result, the USGA now will first tests balls inside. The balls are hit into a net, after traveling through a 70 foot long “tunnel” through which balls are launched from a golf ball launcher that is similar to a baseball pitching machine found in batting cages. At least a dozen balls are tested in as many as 15 different combinations of spin rate and speed. The balls travel through sheets of light called light screens, that measures the ball’s position. When all of the factors are put together, the USGA can predict within 3 yards how far the ball will travel. All done without hitting the ball outdoors. To conform within the rules of golf, the ball must not travel more than 317 yards (with a 3 yard tolerance). Balls that pass all tests for conformance are listed in the List of Conforming Golf Balls, this is published each month on the USGA’s website.
What the USGA does with club testing is different from golf ball testing. That’s because the club head, the shaft and the grip all have to be tested for conformance.
Those guidelines are listed in Appendix II of the Rules of Golf. Most of the specifications are objective, like width and depth of grooves. For groove testing, the USGA uses devices like a protractor or a micrometer. There are more complex instruments like GrooveScan, for measuring groove size or a pendulum test to determine the flexibility of the golf club face, to test club and ball interaction.
The lab at the test center does more than just test the products that arrive and request to be tested, the lab receives and studies results from ShotLink, the data supplier to the PGA Tour for research.
In the course of a year, the center gets over 2,000 pieces of equipment to review each year, including tee’s, gloves and shoes that must conform to rule 14-3 and Appendix IV of the Rules of Golf. The process for testing normally takes about 18 days, and then the manufacturer is notified of the USGA’s decision, if the manufacturer is notified that their submission does not conform, like in the court system there is an appeal process.
The first appeal goes through the Equipment Standards Committee. If the ESC upholds the ruling, submitter can make second appeal to the entire Executive Committee. If that appeal fails to pass, it’s back to the drawing board.
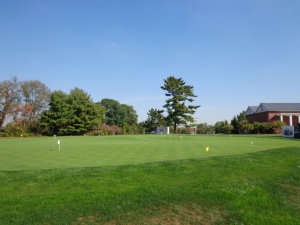
Putters can be tested on the big outdoor putting green ,located between the test center and the golf house museum.
The big outdoor putting green is another way to test clubs for the USGA. Putters get run through the tests the other clubs do, for club head, shaft and grip. But there is nothing like watching a ball roll on the natural surface of an outdoor green, when the USGA does putter testing.
If you’re wondering why all the research, why all the testing, is it really needed. Well the answer is an obvious, Yes.
What the USGA does is to monitor and understand equipment advances and how they affect the evolution and sustainability of the game. The results of USGA testing and research, leads to new equipment rules, and interpretations of test methods. When new rules or test methods are needed to protect the game, the ES Staff follows Equipment Rulemaking Procedures, Version 1.1, that were adopted in November of 2011.
The R&T Center is a certified facility. all work done there is done with strict compliance with the policies and procedures of the Test Centers quality management system.
As a result the next time your purchase equipment or golf balls, you will know what they have gone through just to be on the shelf of your pro shop or golf store.
The USGA, helping keep golf legal, and helping you enjoy this great game a little bit more.
The Gog Blog will return in the days ahead with a look at the USGA Museum, to see some of the great history of golf, stay clicked in with us.